Custom Brims to Combat Warping: A Parametric Solution in Progress
Warping has long been a persistent challenge in 3D printing, especially when working with larger prints or materials prone to shrinkage during cooling.
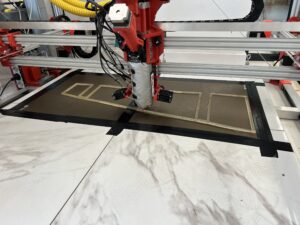
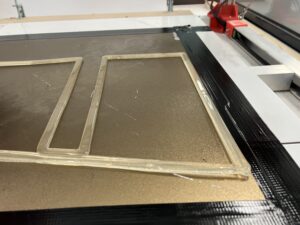
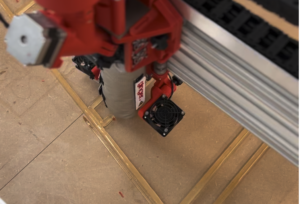
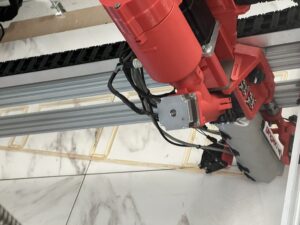
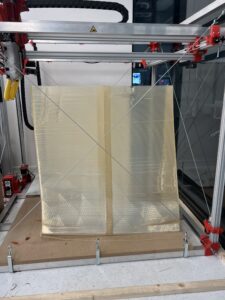
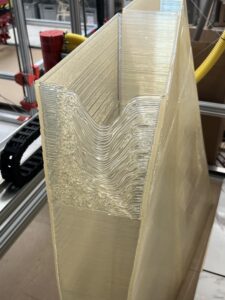
At PARAMETRIC.solutions, we’re exploring innovative approaches to address this issue. One such development is a custom parametric brim designed with additional “mouse ears” that allow physical anchoring to the print bed for enhanced stability. This experimental solution, generated with a Grasshopper script, highlights the potential of computational design to tackle practical problems in additive manufacturing.
The Idea Behind the Custom Brim
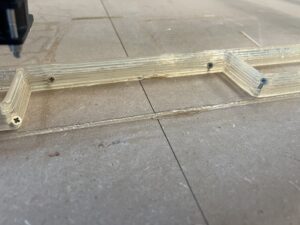
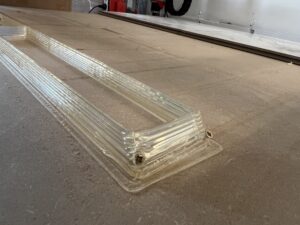
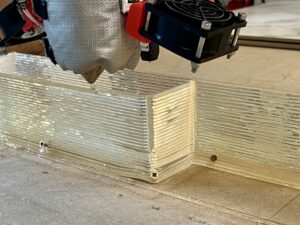
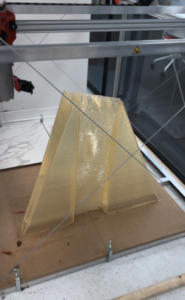
Traditional brims provide a larger surface area around a 3D print to improve adhesion and counteract warping. However, for challenging prints, this can fall short. Screwing that down to the build plate was one step further but the model then is getting destroyed. Our approach, based on a paper, takes the concept further by integrating mouse ear-like extensions into the brim. These extensions feature holes that allow the brim to be physically fastened to the underlying print bed or a wooden board using:
• Screws for direct attachment.
• Clamps for a secure hold without permanent modifications.
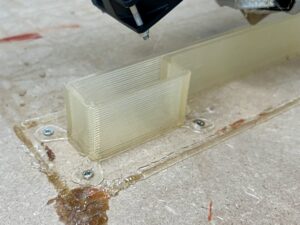
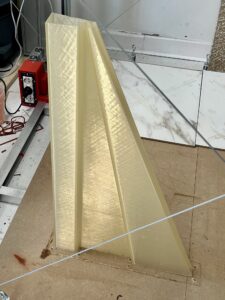
This enhanced connection between the material and the print bed ensures that the part stays in place during printing, even as it cools and contracts. An could look like seen in the animation.
From Concept to Execution
Using a Grasshopper script, we developed a parametric tool that adapts the custom brim to the specific geometry of each print. This allows the mouse ears to be positioned optimally, ensuring maximum stability without interfering with the print itself.
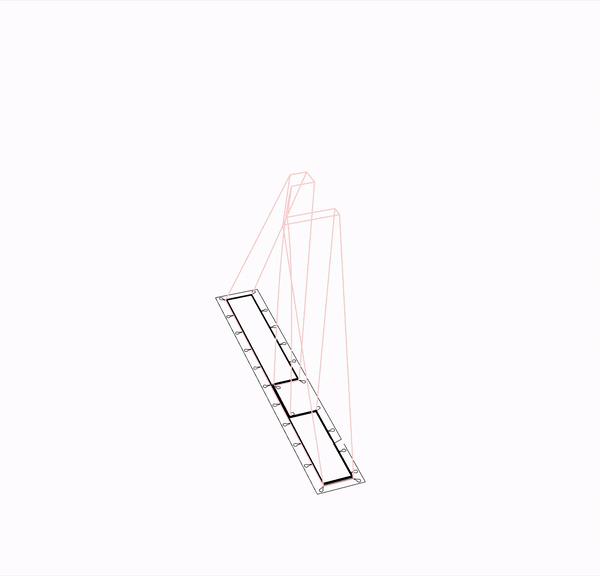
During the testing phase, the system showed promise but also highlighted areas for improvement:
• Initial Success: The physical anchoring significantly reduced warping in some areas, keeping the part flat and minimizing lifting at the edges.
• Unexpected Challenges: In some cases, warping forces were strong enough to damage or even break the mouse ears, suggesting that a single-layer structure may not always be sufficient for more demanding prints.
These findings have led us to explore printing multi-layer mouse ears or reinforcing the structure with additional material for higher durability.
An Ongoing Process
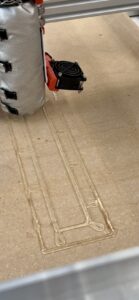
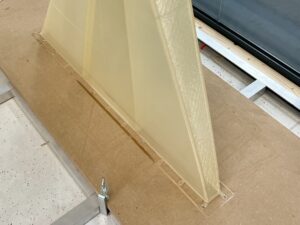
While the custom brim solution is not yet perfect, it represents an important step toward mitigating one of 3D printing’s most common challenges. The adaptability of the Grasshopper-generated model means that adjustments and iterations can be made quickly, refining the system to better handle high-stress scenarios.
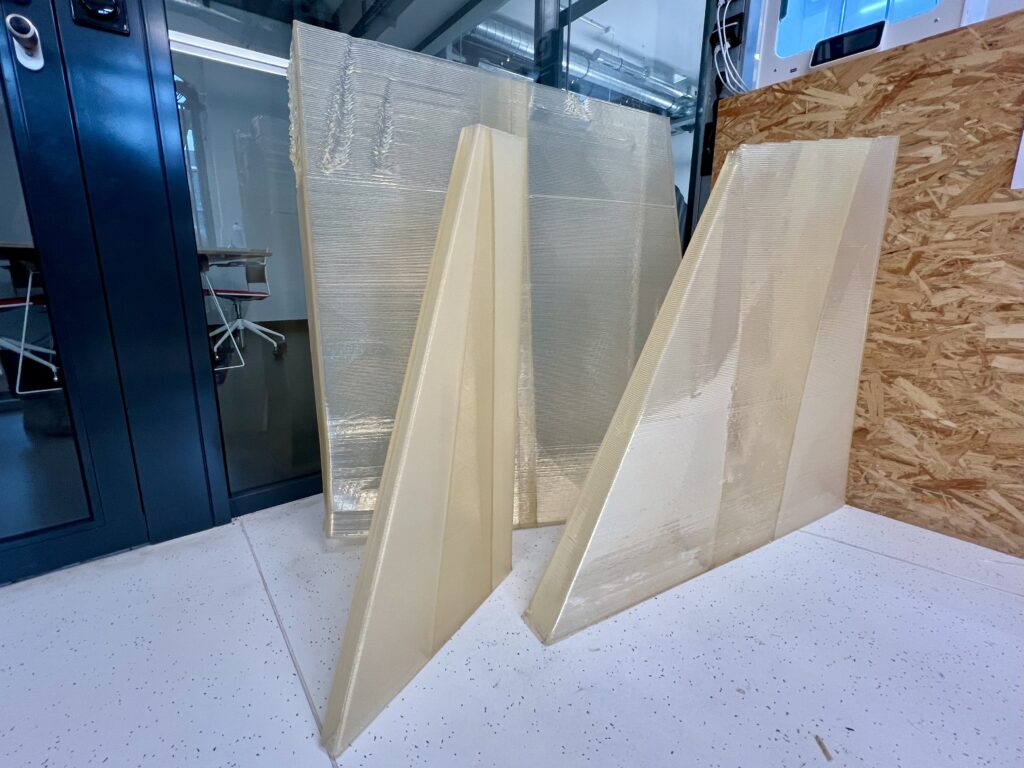
This iterative approach, driven by parametric design, exemplifies how digital tools can create solutions tailored to specific needs while enabling ongoing experimentation and improvement.
Ready to Bring Your Code to Life?
At PARAMETRIC.solutions, we continue to push the boundaries of what’s possible with computational design and additive manufacturing. Our work on the custom brim is part of a broader effort to develop smarter, more reliable tools for 3D printing, addressing real-world challenges faced by manufacturers and designers alike.
If you’re interested in exploring innovative solutions for additive manufacturing or want to learn more about our approach to digital problem-solving, get in touch with us today. Let’s create the tools and processes that shape the future of fabrication.